Abtec’s knowledgeable and experienced team of injection mold experts will engineer your project to your specifications. With over 100 years of experience in plastics engineering, plastics manufacturing, and custom injection mold design services, Abtec offers an assortment of plastic materials, expert assistance with part design, and tooling to create injection mold designs that perfectly match the tolerance and dimensions of any component or part.
The factors that set Abtec Inc. apart from other injection mold companies is the quality of the parts that we make for our customers that include uniform wall thicknesses, consistency, professionalism, and exceptional quality and reliability. Abtec’s many years of success is due to the satisfaction of our customers who are our partners in a long term and successful relationship.
Designing a Plastic Injection Mold for Your Business
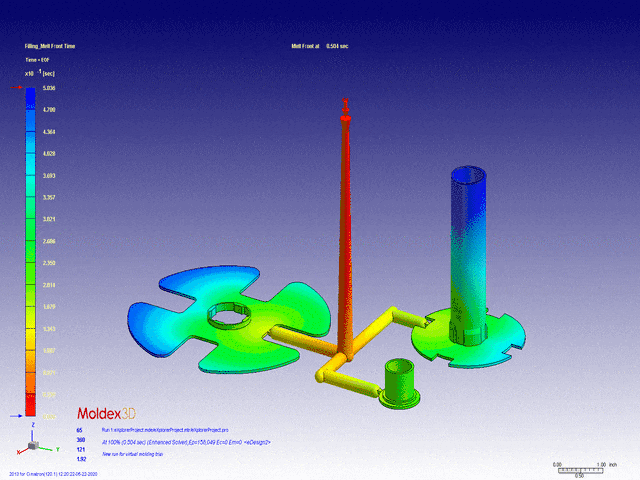
Injection molding uses thermoplastic resin pellets, which are melted and injected into a mold then cooled to create a flawless uniform plastic shape. The success of the process depends on expertise, knowhow, and experience. Each aspect of a mold must be engineered with precision, care, and attention to detail to ensure dimensional accuracy and tolerance. Abtec takes a great deal of pride in each step of the process, which are carefully monitored by Abtec specialists and engineers.
As with any type of manufacturing, planning plays a significant part in the success of a process. This is especially true in the injection mold industry where each step, from the selection and preparation of the resin to the cooling of the final product, is timed, measured, and monitored to ensure the highest quality. For Abtec, each of these procedures are a requirement and necessity to a quality part.
There are several factors in the injection and cooling stages of the injection mold process that affect its quality and repeatability. The adherence, by the experts at Abtec, to fundamental injection mold design services’ guidelines ensures the success of all products produced for our customers.
The engineers and designers at Abtec realize that our established experience as a molder streamlines the design process and builds a stable partnership that guarantees our customers a quality product. Abtec builds the tooling and use the techniques that best fit our customer’s requirements and the specifications for their design. The experts at Abtec carefully review the injection mold parameters to provide unique solutions for any product problems.
The key to success in the 21st Century includes the use of the many technological advancements and procedures that lower turnaround times and increase efficiencies. To meet the challenges of modern manufacturing, Abtec has invested in the latest methods for designing, crafting, and engineering our molds, which allows us to offer our customers high tech services at a reasonable cost.
Using modern mold making processes, Abtec can quickly respond to the requirements of our customers to produce precision, custom injection molds in the shortest amount of time. Our staff of experts work with our customers to analyze projects, develop solutions, and identify opportunities to save money and time.
Our Plastic Injection Mold Design Services Work With Numerous Formats
Abtec’s injection mold design services department uses a variety of CAD formats, including:
- CimatronE
- SolidWorks
- ProE
- AutoCAD
- CADKey
Abtec relies on 3D CAD, such as CimatronE, for the development of designs and manufacturing processes. The features of computer design make it possible to create a rendering of an injection mold with an image of the dimensions, tolerance, shape, and form of the final product for examination, adjustments, and approval. As with many of the other organizational factors at Abtec, the CAD process saves time, money, and eliminates concerns regarding production errors.
Modern design engineering offers an assortment of computer tools to create 3D images of a product. The selection of the format depends on several factors including the complexity of a design, its dimensions, and its specificity. As Abtec has grown over the years, we have taken advantage of the available technological choices that best fit the demands of a client’s component. Our understanding of the many computer formats gives us an advantage over other injection mold companies and makes it possible for Abtec to custom engineer any part or component. Our goal is to use every available resource to ensure the injection mold products we produce meets the demands of our customers.
Computer formats are constantly being updated and changed as new technologies are introduced. Abtec’s team of engineers and designers work diligently to ensure we have the latest and most up to date software including such programs as CimatronE, Pro/ENGINEER, CADKey, SolidWorks, and AutoCAD.
Included in Abtec’s library of computer tools are design formats such as:
- IGES
- STEP
- DXF
- DWG
- Parasolid (x_t)
- STL
The use of this wide array of tools makes it possible for Abtec injection mold design services to work with a client’s drawings, sketches, models, parts, and existing molds to produce the right part at the right cost. As with many parts of Abtec’s goal of complete satisfaction, we work to guarantee the parts we produce are the perfect part for a client’s application.
Process for Reviewing Plastic Injection Molding Designs
A necessary part of injection mold design services is a review of a design to ensure it meets the necessary requirements. Although it may be viewed as a quality check, in actuality, it is the final examination of a design such that it meets Abtec’s high standards and fits the parameters of the client’s needs. Every injection mold process involves a set of steps that are closely followed and reviewed such that they meet company specifications. Plastic injection mold design services review is organized to monitor every step of the injection mold process.
-
Overview
- The overview is in regard to the type of mold that needs to be crafted and machined. While the material for the mold is standard, there are aspect of the mold that have to be carefully considered in order to reach the appropriate dimensional criteria. Cavitation, mold construction, and tie bar distance are some factors that engineers consider during the overview process.
-
Parting Lines
- Parting lines are a crucial part of the development of the format of a mold and are determined by the shape of the product, parting sequence, and parting method. Abtec engineers define parting lines at the beginning of the design process in order to limit the amount of secondary machining an injected part may require.
-
Injection
- Injection is the process by which the melted plastic resin is placed inside the mold. The method that is chosen is influenced by the position of the parting line and the orientation of the mold. While hot injection is one of the more common injection methods, there are certain types of injection mold products that can be better served by cold injection. This particular aspect of the injection mold process is determined by the computer rendering and includes the type of gate, its size, and its location.
-
Venting
- Venting is an important part of mold design since vents allow air to escape as the mold is filled. The strategic placement of vents ensures the quality of the molded product and the smooth flow of the plastic resin. In mold design, the location of the vents is closely examined with the general rule being the placement of vents opposite of the gate. Other placements of vents may be necessary and are determined by the type and design of the mold.
-
Cooling
- During cooling, an injected molded product solidifies and assumes its shape. The length of cooling time varies in accordance with the product being molded and its complexity. The factors that affect cooling time are the part geometry, the type of plastic material, the shape and size of the mold cavity, the wall thickness of the part, and the heat required for the injection process. The accurate calculation of the cooling time is crucial for part quality and a basic part of Abtec engineers’ overview.
-
Ejection
- When the plastic component in the mold has cooled sufficiently, the part is ejected from the mold. The appropriate ejection method depends on a variety of factors, including the number of ejection stages, whether it will be accomplished by pushing or pulling, the surface contact between the pins and the mold, the required clearance, and the desired mechanical properties of the product.
-
Closing
- After the part is ejected from the mold, the mold process repeats. For the process to restart, technicians consider the ejection sequence, any impediments, and the ejector system return method. Although the alignment of a mold can be assumed, it is of particular importance to check the closure of a mold to ensure that it is aligned properly.
-
Handleability
- Injection molding relies on precision, accuracy, and the ability to properly measure dimensional geometries. These factors necessitate a close examination of molds to determine if there is any wear, deformities, or irregularities. In most cases, molds can last for hundreds of thousands of cycles without any errors. The pride that Abtec takes in the quality of its products requires close examination of every part of the molding process, including the condition of the mold.
-
Safety
- As with all manufacturing processes, safety is paramount in the injection mold industry. Every part of injection molding is examined and considered when addressing safety issues. At Abtec, the safety of our highly trained personnel is of the utmost importance and is monitored from mold making to product completion. Professionalism is the foundation of Abtec Inc. We have spent many years perfecting and honing our processes such that they are safe, reliable, and efficient.
What Our Certified Injection Mold Designers Can Do for You
At Abtec, our highly skilled team has over 100 years of combined experience designing, developing, and manufacturing custom injection molds and support tooling. Our state-of-the-art manufacturing facility and advanced injection molding equipment offer complete technical and engineering support to create durable molds that offer repeatability and provide exceptional consistency. Abtec’s team of injection molding design services experts follow every step of the manufacturing process from part conception and computer design to mold making and product shipping. This devotion to quality is what has made Abtec a world leader in the injection mold industry.
In Addition to Designing Plastic Injection Molds, Abtec Also Offers the Following:
For Professional Injection Mold Designs and More, Call Us Today
As a leader in the injection mold industry, we at Abtec Inc. take pride in the skill and abilities that we offer to our clients and customers. It is our deep concern for the quality and the needs of our customers that has set us apart from other injection mold companies. Over the years, Abtec has developed strong relationships with our customers who have become our manufacturing partners. They depend on Abtec quality to ensure their products are produced to perfectly meet their stipulations and requirements.
The experts at Abtec have faced many challenges in the development of their expertise and have produced molded plastic products in a wide assortment of shapes, sizes, and configurations. Regardless of the demands of our clients, Abtec professionals have taken the necessary extra steps to ensure that our customers receive the highest quality of service.
Abtec professionals can take any design and turn it into a workable product. The foundation of our business philosophy is to face engineering challenges with an open mind and provide practical, cost saving answers. The team of experienced Abtec designers is ready and waiting to meet any injection mold problem you may have.
To learn more about the injection mold design services at Abtec, contact us today at 215 788 0950 or email: sales@abtecinc.com. Our team of professionals are ready to help develop your injection plastic mold designs and introduce you to our superior service. If you have any questions, feel free to check out our FAQ page for answers. We, at Abtec, are here to provide the expertise, knowledge, and professional guidance you require.